A few years ago, we undertook the renovation of a residential property. The three-bed apartment “Architects Abode” was opened up and converted into a spacious and sun-filled modern two-bed family home. During the renovation, we used mustard yellow Jaisalmer stone for the flooring throughout the apartment. Laid in a chevron pattern with brass inlays, this pattern involved a certain amount of wastage. Our commitment and belief in sustainability and no wastage saw us collect the leftover uncut pieces and put them away, waiting for the time when we can find a new use and re-purpose them.
A recent office move gave us the opportunity to re-arrange our working space and move away from the clinical corporate white office environment we often find ourselves spending so much time in.
We wanted a functional yet warm and comfortable space to work and create in. Being based in India means that we can easily get workers at a short notice. A fleeting idea at best, in almost no time can be realized here, as in our case.
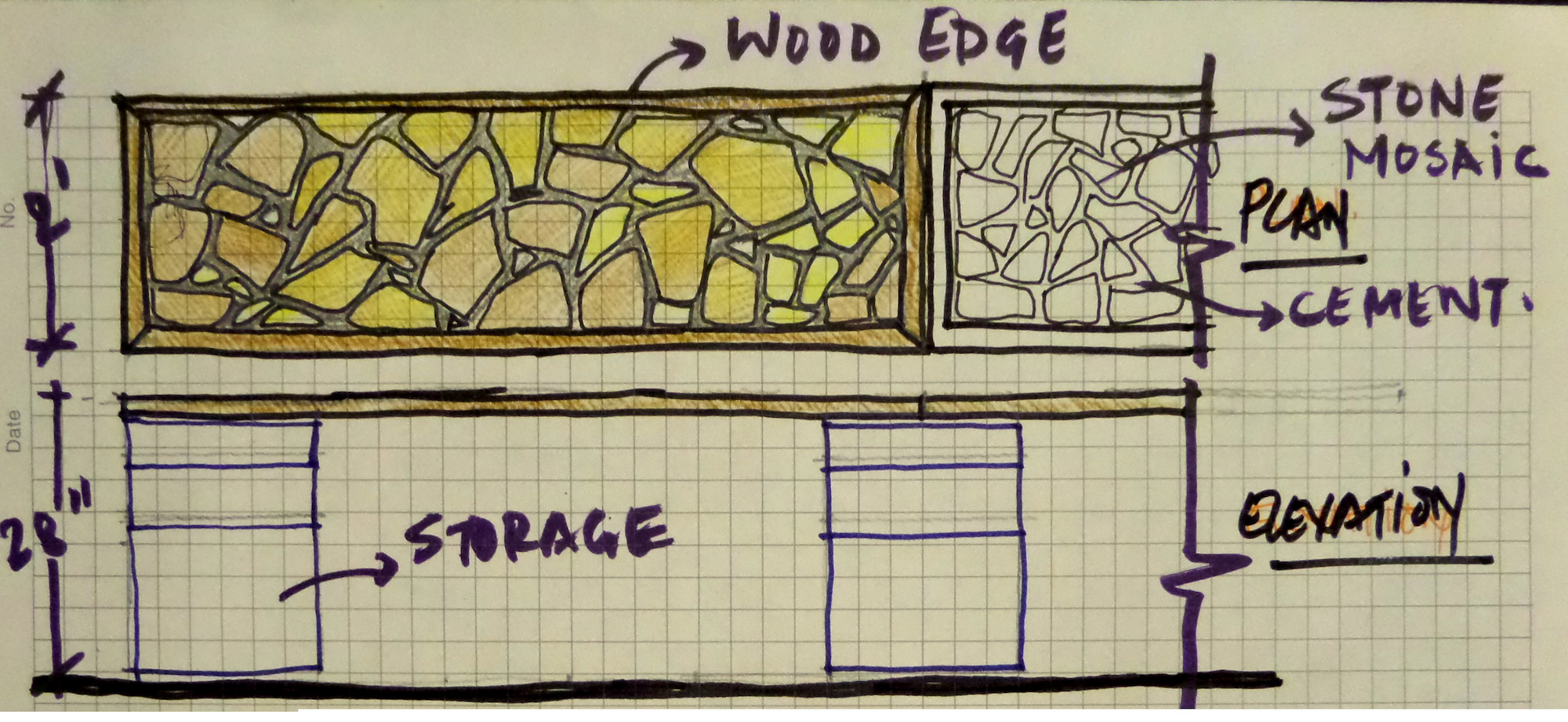
Mosaic Layout Sketch
An easy way to re-purpose stone offcuts, is to create a mosaic. So we thought we will do just that, except not as it is commonly used as a floor, but instead, make panels that can cover the work counters in the new office. Knowing how mosaic behaved, fashioning work tops had its own share of idiosyncrasies…
Usually, the stone will be cast in a bed of mortar as a floor, or as part of concrete slabs to work as counters. But if it were to be cast in concrete as counters, it would prove to be heavy and non-transportable, if and when we moved office again.
If we stuck the pieces onto a board, we felt that it would not seem authentic and honest, and the polishing process would destroy the substructure.
And so after pondering for days we finally came upon a viable alternative.
The stone pieces were stuck with Araldite adhesive upon a cement based bison board and block board sub-structure.
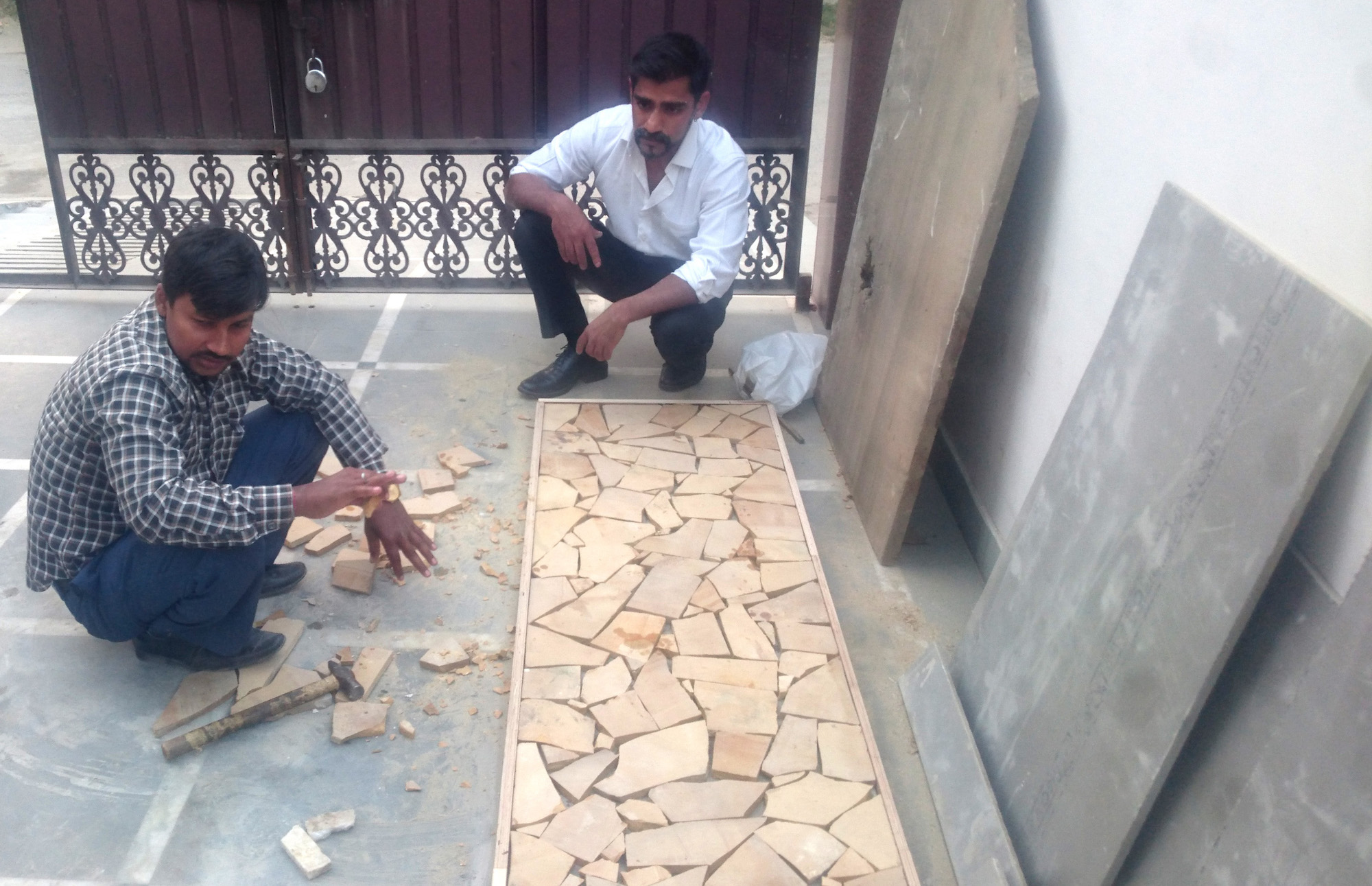
Jaisalmer stone pieces are stuck to the bison board panels by our head stone mason ‘Ashok Pandit’
He cannot fathom why we cannot use a laminated board as a work counter instead of stone mosaic.
The panels were shuttered from the sides and cement slurry was poured over the mosaic pattern.
The cement slurry takes about 24 hours to harden and form a monolith with the stone pieces. As this is an exothermic reaction, there is a certain amount of contraction of the material, leading to indentations and imperfections in the surface of the joints. Once dry, we refill the indentations with the same material.
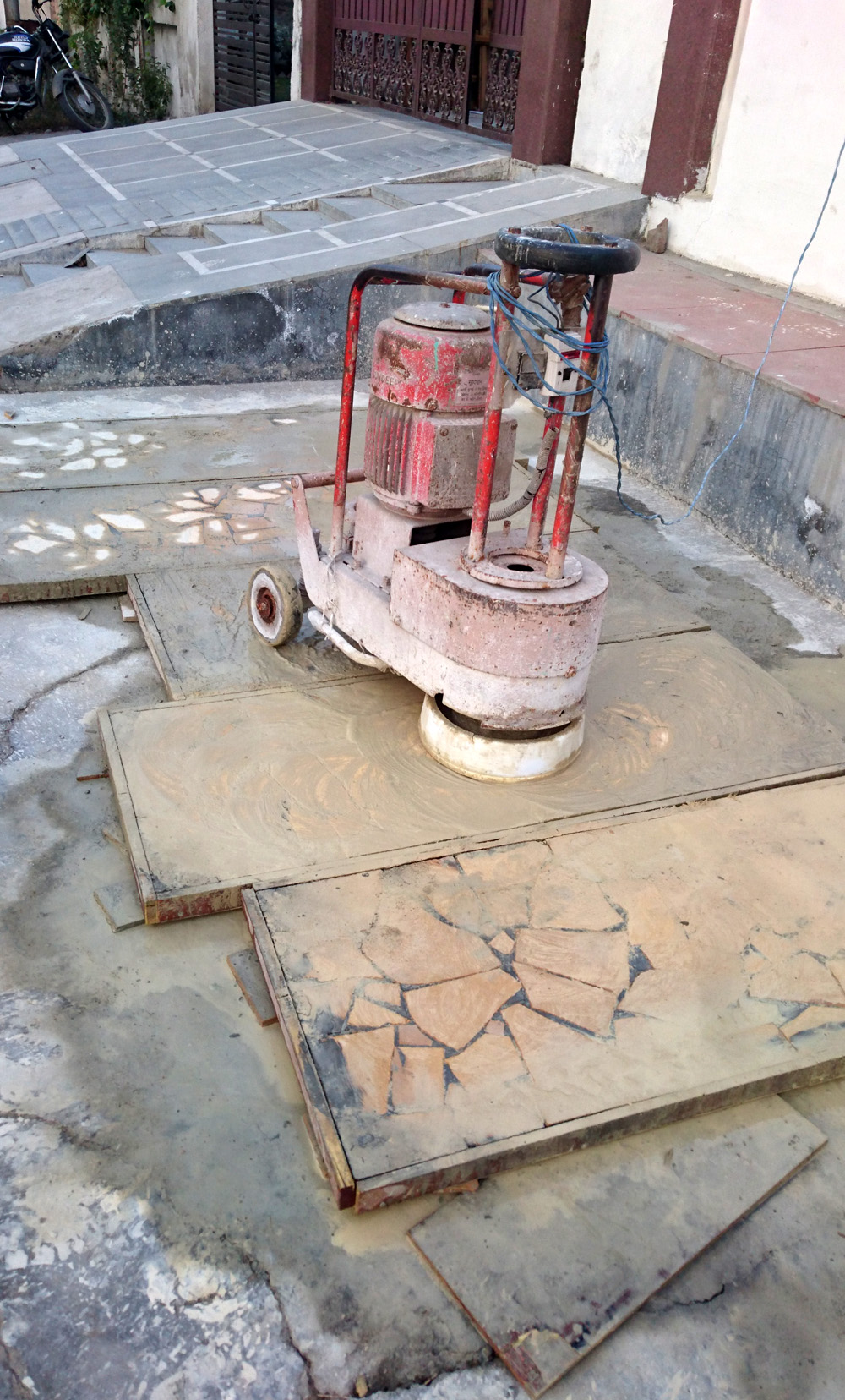
The grinding machine levels our counters.
When the cement is set, the panels are ground, to level out the surface.
This happens with the help of a seven stone grinder machine, used to cut and polish the mosaic, giving us a flush level surface.
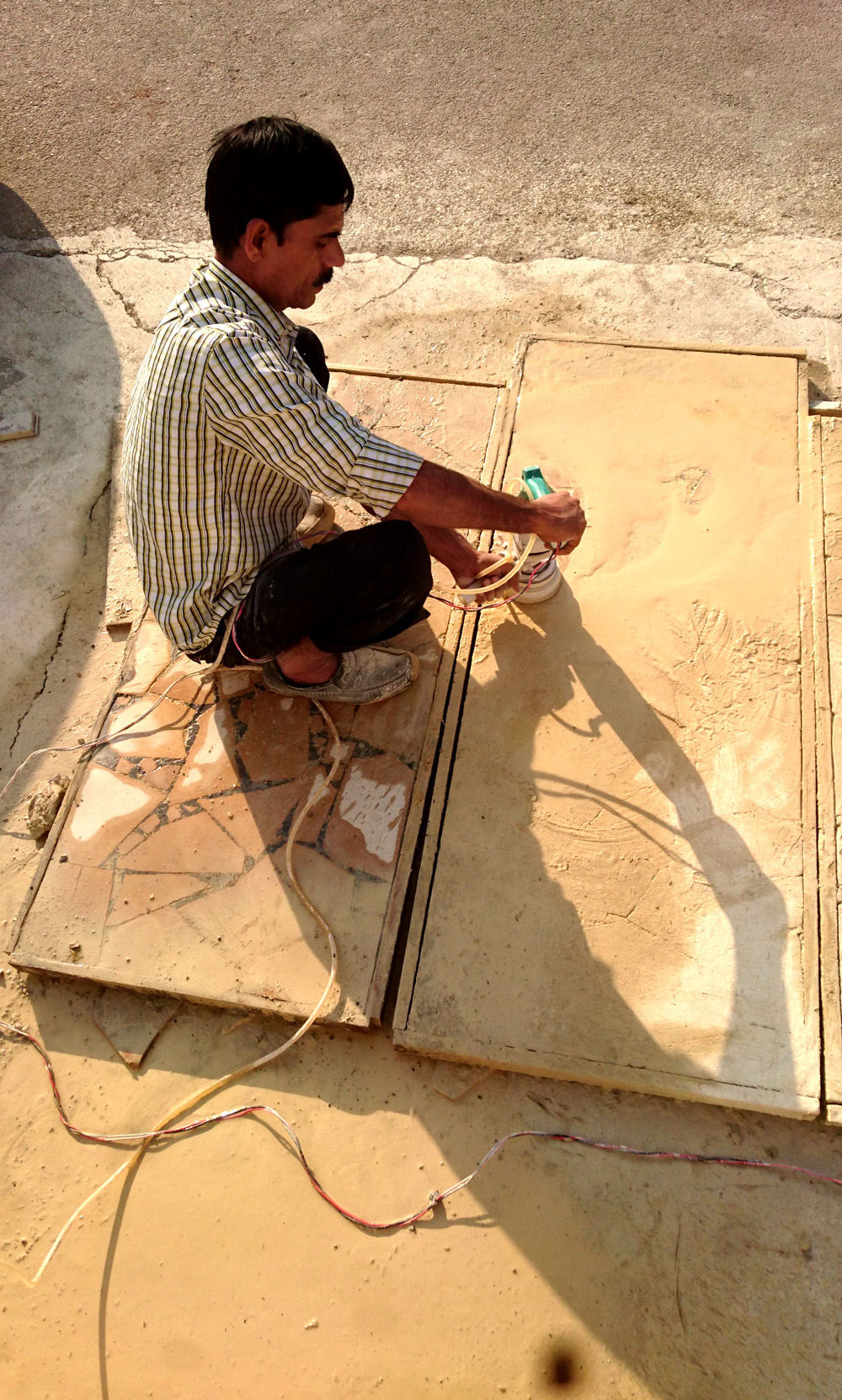
Stone mason is a picture of concentration as he carefully grinds the corners with a smaller machine so as to prevent chipping of the edges.
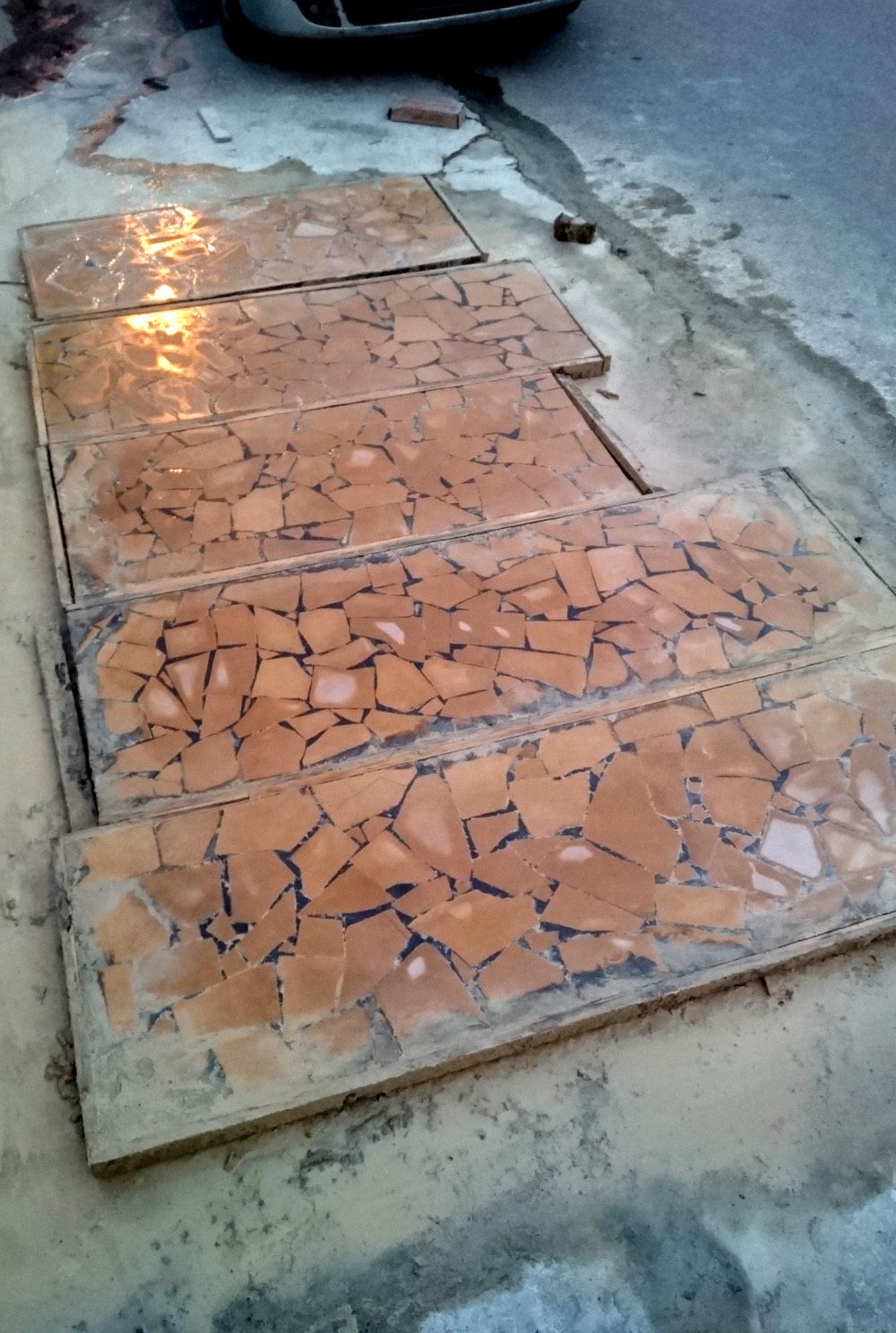
The panels have been ground and honed, ready to be repaired with ‘tenax’.
Tenax filler glue is used to horizontally repair and rebuild and fill all the imperfect joints.
Tenax filler is a semi-solid consistency that is smooth and easy to spread. It is used to fill holes in stone and will accept a polish, and is usually recommended for interior use.
Once covered with Tenax, the panels are left to dry for 48 hours.
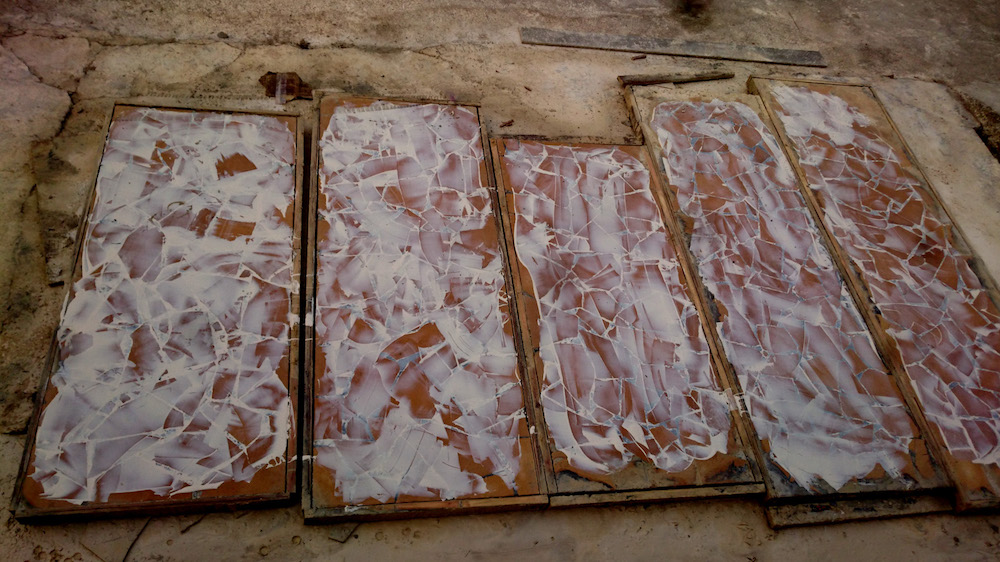
The stone filler and glue ‘tenax’ forms a layer over the panels filling all crevices and indents.
And then ground once again with a machine to remove extra bits of filler.
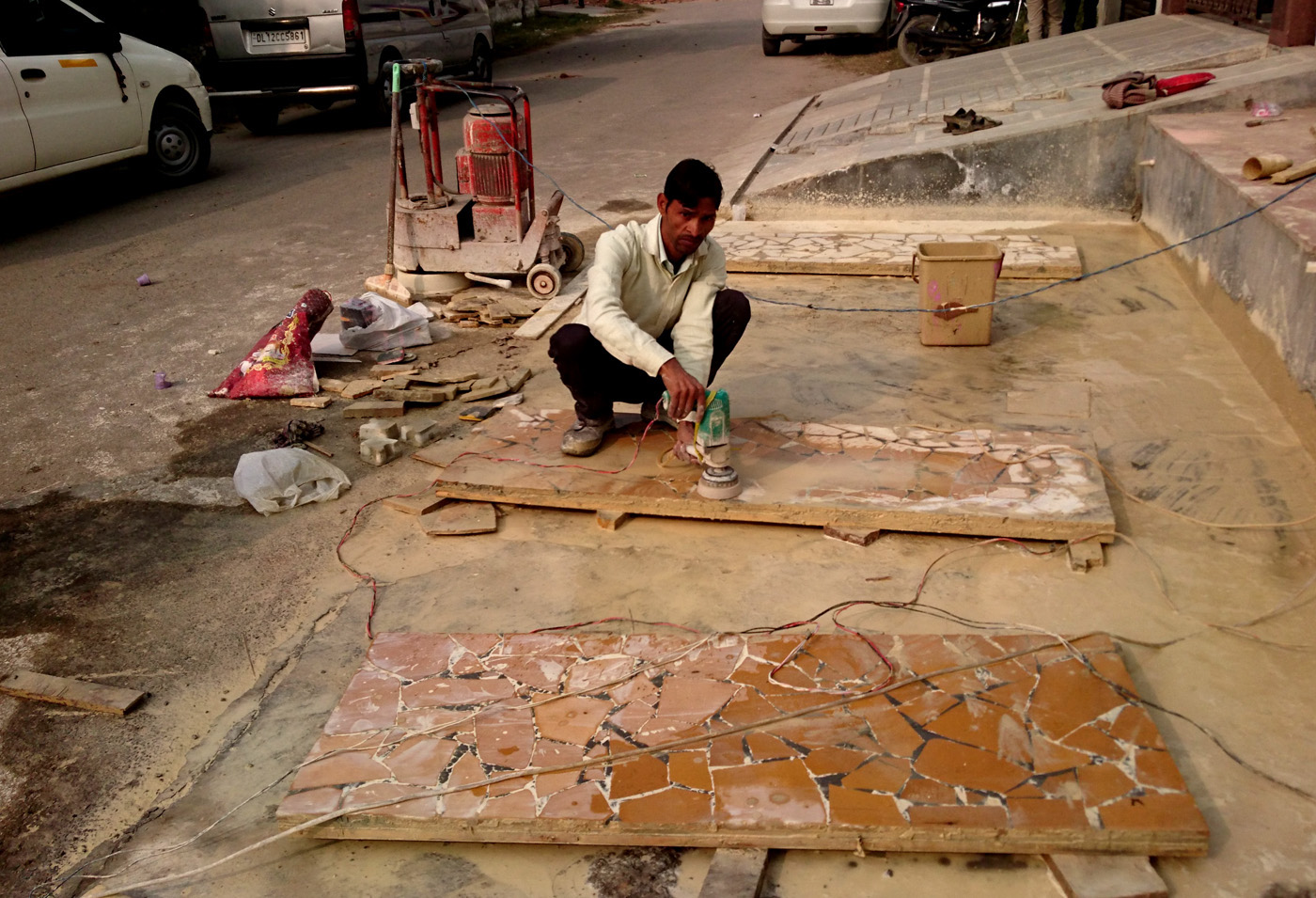
The Tenax repaired panels are now ground to finer smoothness with blades 6 and 7
To obtain a random coloured filling, no pigment was used with the Tenax filler, thus giving us a finished look that looks perfectly imperfect.
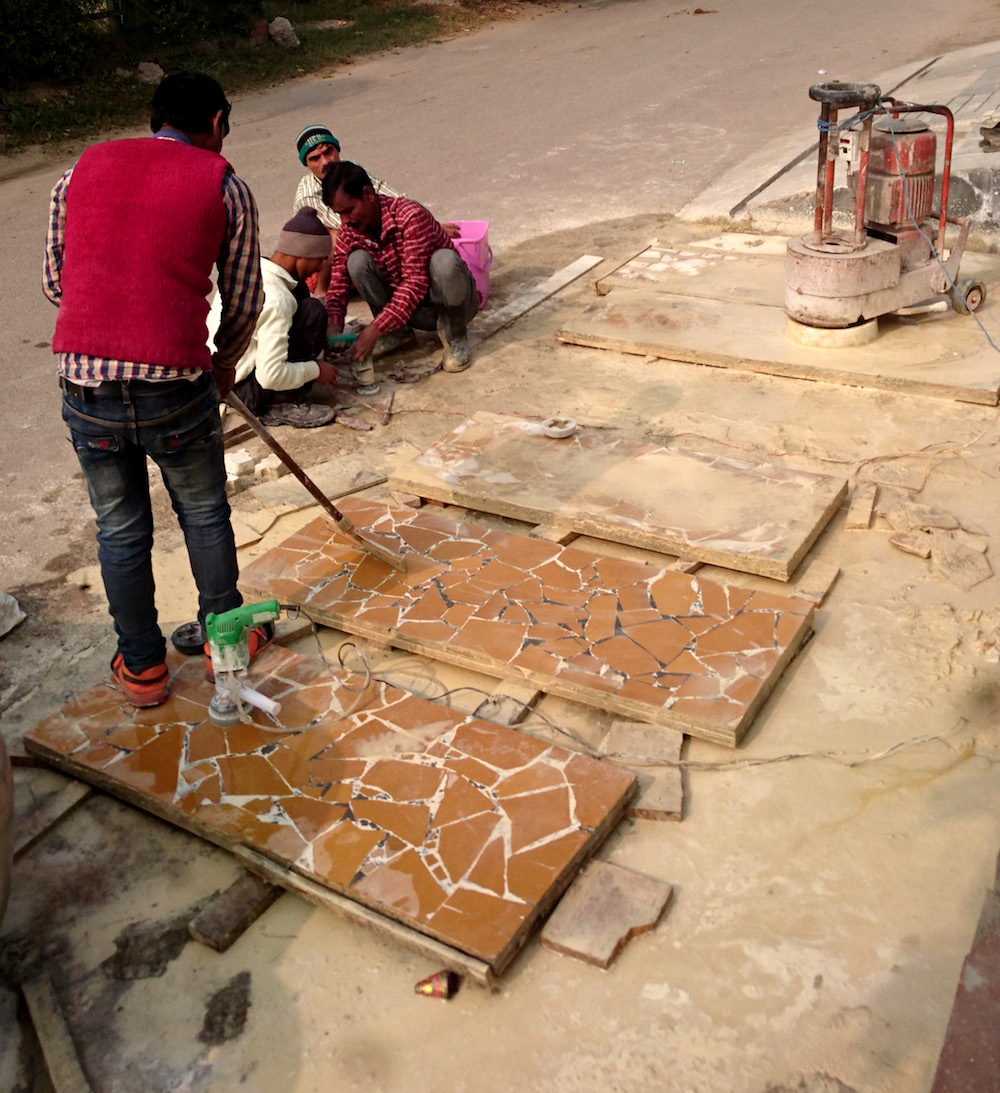
Frequent stoppages for repairs of their machines, notwithstanding, Hemant diligently takes time off to clean the surface of the mosaic panels
Once polished, the panels were edged in wood and ready to be installed.
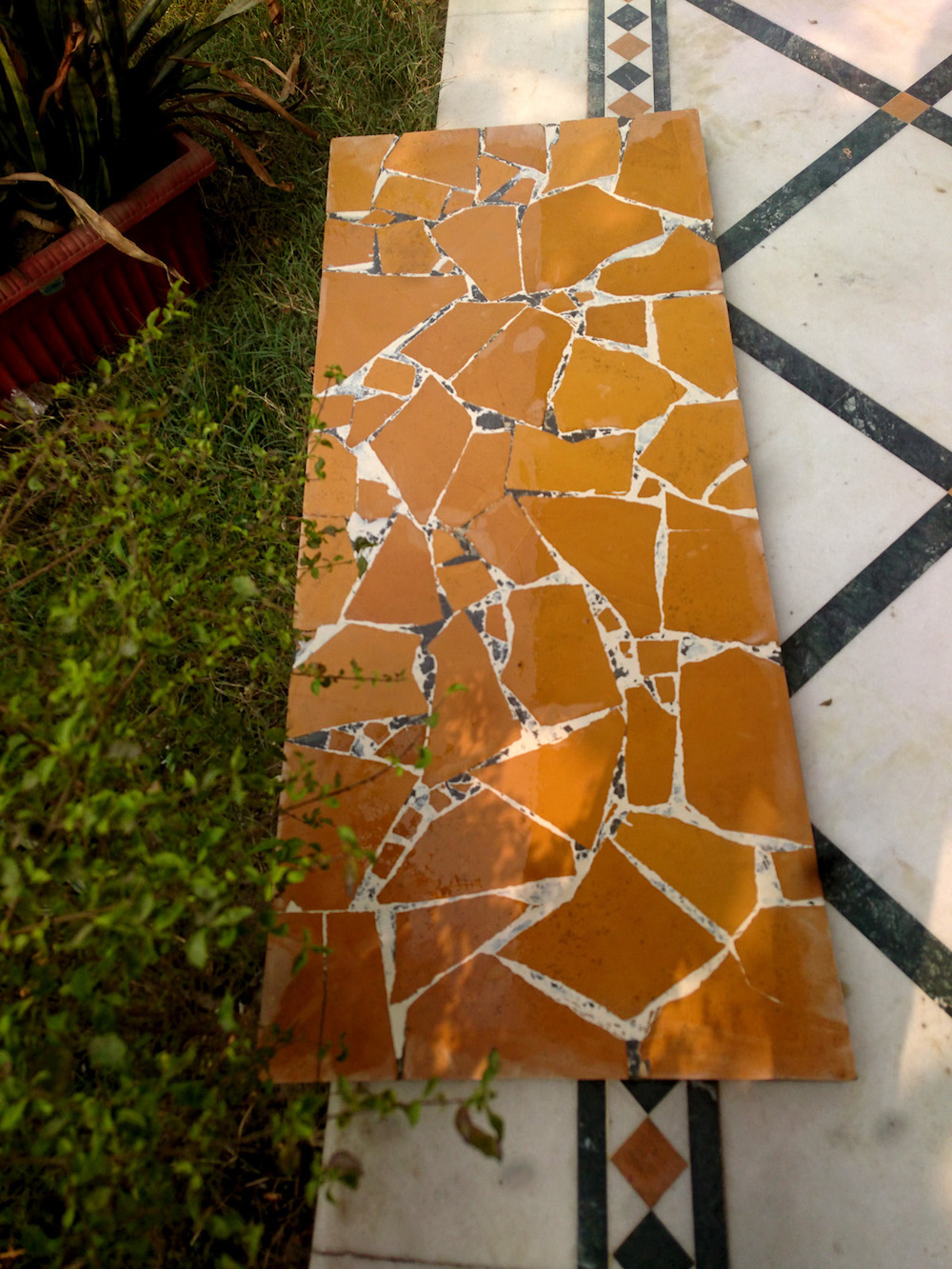
The panel is now ready to be edged with wood and installed on site
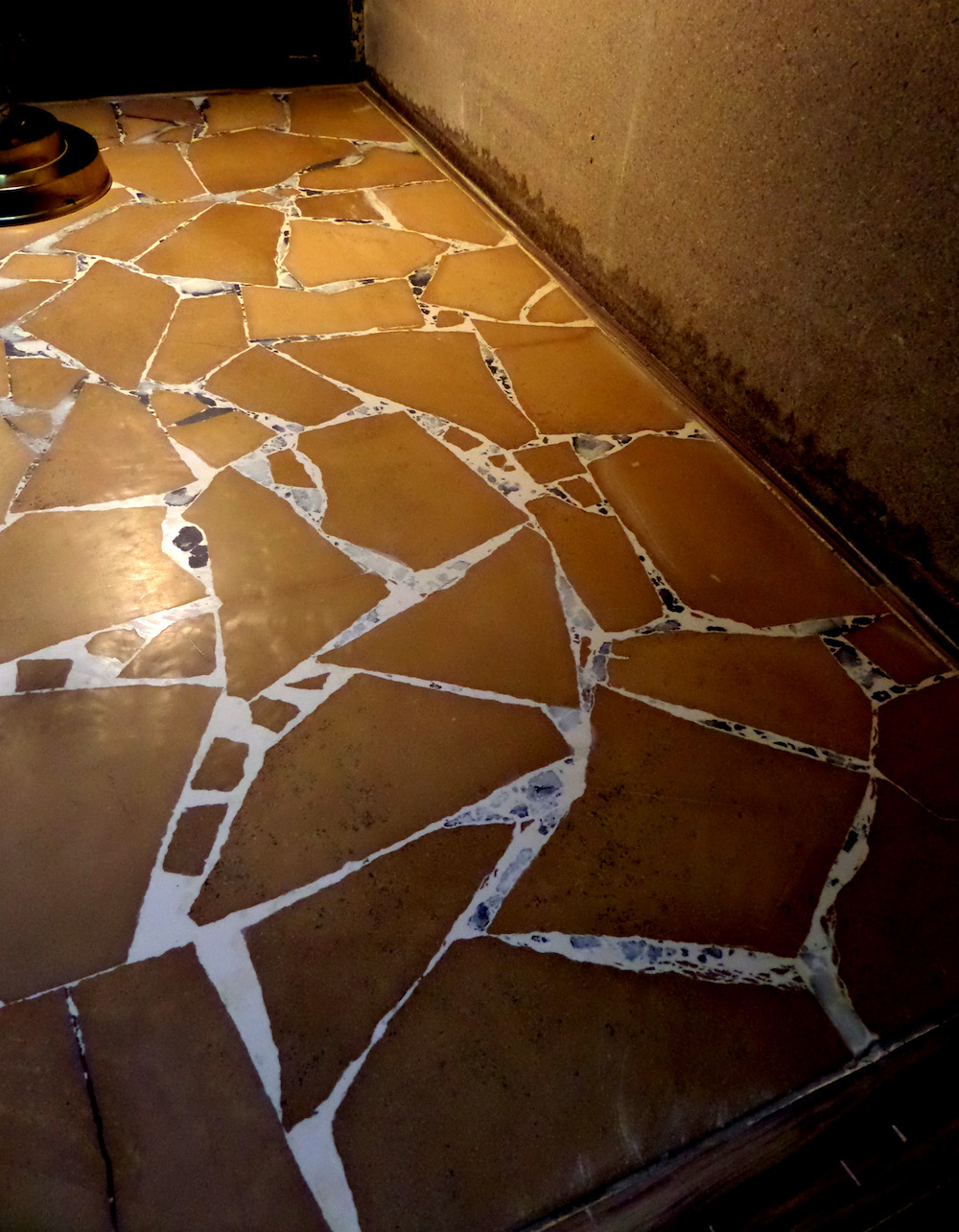
Our masons frustration: “Why do we want this discolouration of the joints? Why not one uniform grey colour ?’
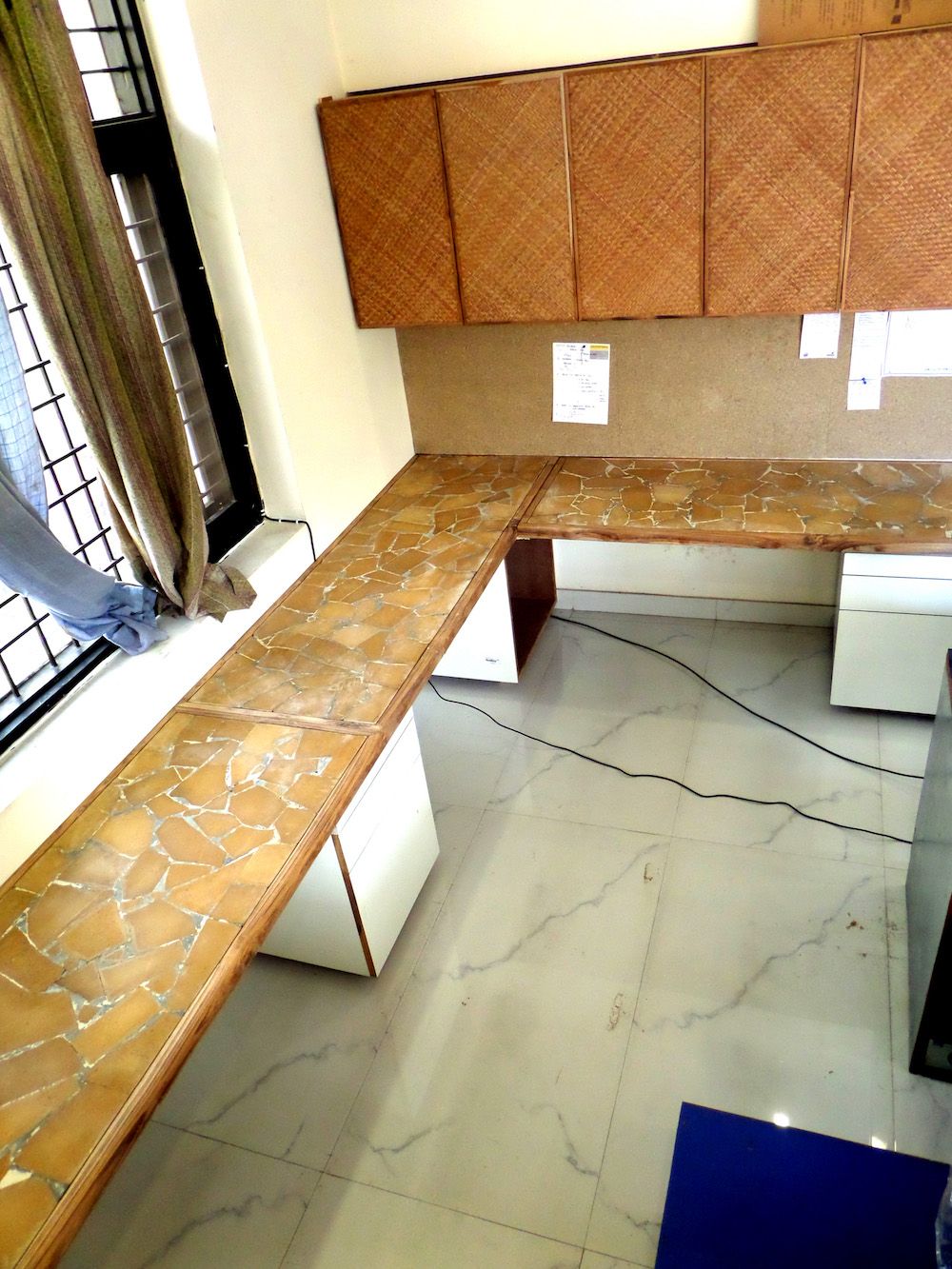
Jaisalmer stone mosaic panels finished and in place